廃棄物処理業から燃料製造業へ。成功の鍵は地域との連携。
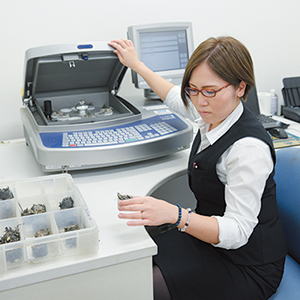
15分に一度、サンプルをとって分析器にかける。
エネルギー資源に乏しい日本。新エネルギーへの取り組みはとりわけ東日本大震災以降、官民で多様なチャレンジが行われている。また、大量生産・大量消費・大量廃棄型から循環型社会への移行についても社会的課題として幅広い分野で取り組まれている。その二つにユニークな技術でアプローチしている企業が静岡県で廃棄物の収集・中間処理を手掛けるリサイクルクリーンだ。同社は、そのノウハウを活かし、RPF(廃棄物を利用した固形燃料)の生産に力を入れている。
代表取締役の藤城太郎氏は、取り組みを始めたきっかけをこう語る。
「2011年の東日本大震災を機に太陽光発電やバイオマスなど再生可能エネルギーが注目されるようになりました。政府がFIT制度(固定価格買取制度)を取り入れ、廃棄物を燃料化する機運が高まったのです」
FIT制度とは、再生可能エネルギーで発電した電気を電力会社が一定価格で一定期間買い取ることを国が約束する制度だ。
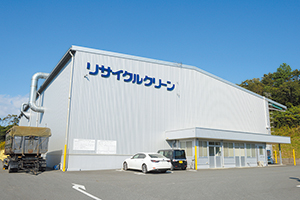
近隣住民の理解が得られ
24時間稼働を実現している。
あるときRPFの全国組織である一般社団法人日本RPF工業会から藤城氏のもとに入会の誘いがあった。同社では試験的にRPFの生産を手掛けていたが、規模はごく小さかった。会合に出席してみると、大規模で本格的に取り組んでいる企業ばかりだった。
「当社は入会するのも恥ずかしいくらいの規模でしたが可能性は感じました」
同社は建設系の廃棄物をはじめとして、さまざまな廃棄物を集めて分別などの中間処理を行っている。廃プラスチックや木くず、繊維くずなどに分類して、埋め立て処分場や焼却施設に引き取ってもらっていた。
「その中には原料にできるものが結構あるのではないかと考えました」
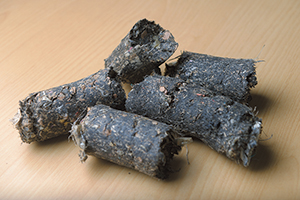
低価格な再生可能エネルギーとして
注目を集めている。
固形燃料を内製化すれば、資源を無駄にせずにすむ。ただ、使ってくれるところがなければ意味がない。日本RPF工業会によると、地元の製紙会社で固形燃料を利用したプラントを新たに立ち上げるという。静岡県の富士市には製紙会社が数多くある。木くずなど自然由来の廃棄物燃料を使って発電するバイオマスボイラーが以前から利用されており、理解があった。
藤城氏は手を挙げて、プラント建設のスケジュールに合わせ、3年計画でRPF専用工場の建設を準備した。14年のことだ。
想定外のトラブル発生。専用建機を設計し乗り切る
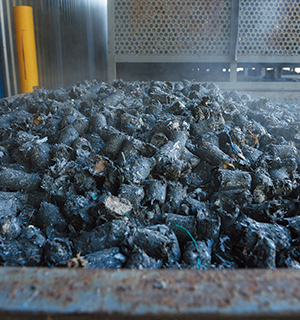
高温で加工しているため、湯気が立ち上っている。
これは、廃棄物処理業から製造業への進出を意味する、大きな転換だった。これまで費用を支払って廃棄物の処分をしてもらっていたが、自ら商品化して販売する。RPFはJIS規格の対象となっており、塩素濃度や熱カロリーなどの厳しい基準をクリアしなければならない。また、利用する製紙会社は成熟産業で、爆発的に需要が増えるとはいえない。高品質を確保しながら、価格を抑えなければならない難しさがある。
本格的な設備が稼働する前に、練習のために10分の1の規模の設備を導入して試験稼働させてみると、思わぬトラブルも発生した。
「重機で廃棄物を投入するのですが、そのフィルターが埃で目詰まりしてしまうのです」
それまでもある程度の埃は出ていたが、粒子がより細かくなり埃の質が変わっていたのだ。そこで建機メーカーのコマツから10名を超えるスタッフの派遣を受けて、RPFに対応できる重機を共同開発した。いまはコマツのカタログにも掲載されている。
また、一口にプラスチックといっても、低温で溶けるものもあれば、溶けにくいものもある。溶けやすいものが多くなれば、固まりにくくなる。それらをうまくブレンドしなければ、固形燃料にはできない。
鉄くずをリサイクルして再び鉄として使うようなマテリアルリサイクルの場合には、廃棄物をいかに分別するかが重要になるが、固形燃料として使うには、さまざまな素材をいかにブレンドして燃料に向くものをつくるかが重要になる。
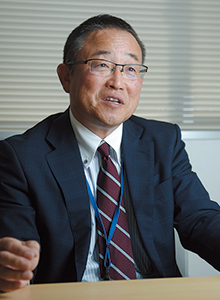
廃棄物を資源として捉え、
埋め立て処分や単純焼却処分を
極力減らし、リサイクル率を向上
させることで循環型社会の形成を
目指している。
品質のチェックは厳しい。
「トラックで納品すると、製紙会社では必ずサンプリング調査を行います」
その結果は毎月一覧表にされ、塩素量や水分量などが一定の範囲内に収まっていなければ、改善を求められる。だから製造工程でもチェックが欠かせない。同社では15分間隔でできてくる製品をサンプリングして、分析機にかけて確認している。分析器だけでも500万円する。
新工場や設備への投資額を計算すると莫大な額になるが、藤城氏には綿密な計算があった。
現在同社では毎月1800トン程度のRPFを出荷しているが、そのうち700トン程度は、各工場から発生する可燃物を利用している。
「こういったビジネスの失敗パターンは工場を先につくってしまうこと。いざ稼働させてみると材料が集まらないから、ダンピングして集めることになるのです」
同社は、それまで有料で処分を委託していた廃棄物で半分程度の材料が賄える見通しが立っていた。不要になった処分料で設備投資は賄える。一方で製紙会社に1500トンほど納入できる約束があったので、参入前から入り口も出口も明確になっていたわけだ。
問題はうまくつくれるかどうか。中間に入る同社が機能しなければ、リサイクルが成り立たなくなってしまうから責任重大だ。だからこそ、本格稼働前に小規模な設備でノウハウの蓄積を重ねたわけだ。
大型化と24時間稼働で製造コストを削減
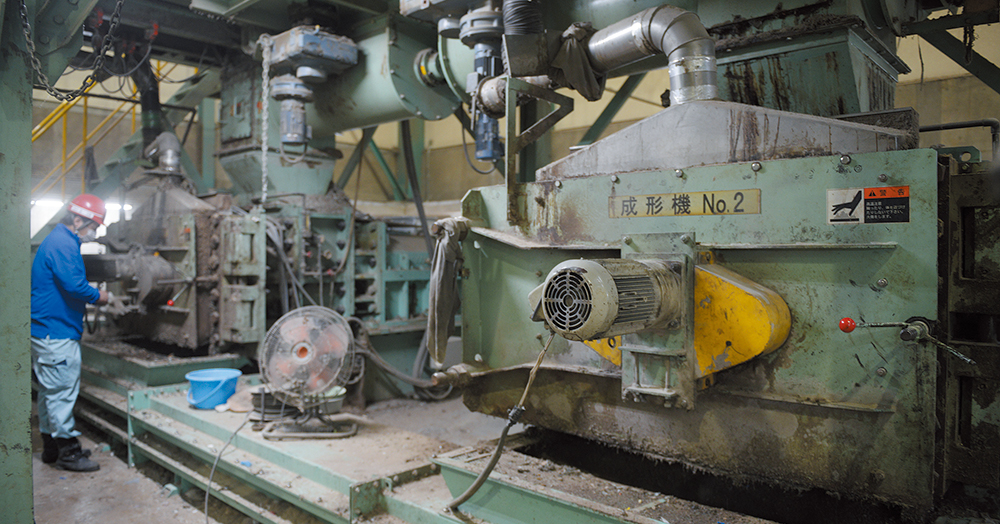
RPFの七つの特徴
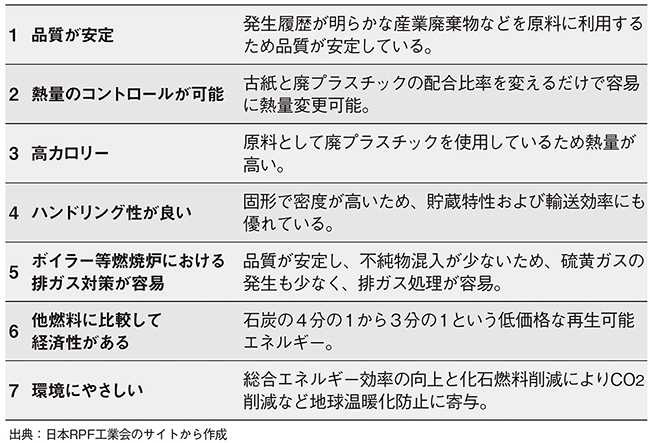

収まっているが、台風の停電で欠けてしまったことが
ある。すぐに注文したが、1000万円かかる上に
受注生産で1年かかるという。その経験を生かして
以降は、予備部品を買い集めている。
右)原料は重機でRPF製造設備に投入するが、
粒子の細かい埃が発生するため、フィルターが
目詰まりしてしまう。コマツとの共同研究で
RPF対応重機を開発した。
製造業に進出するからには、コスト削減も大きな課題になる。
「基本は設備を大型化して長時間稼働できる環境を確保することです」
通常は1時間当たり3・5トンの製造能力がある機械を1台設置するが、同社は並列で2台設置して大型化し、毎時7トンの製造能力を確保。これを24時間稼働させることで、製造コストを削減することに成功した。
これは地元の理解が得られたからこそ実現したものでもある。廃棄物処分業の場合、民家がある地域では1日8時間しか稼働できない。同社の袋井工場は民家から離れているが、地元の承諾が得られなければ24時間稼働はできない。許可がとれたのは、06年の建設以降、地元との友好関係が出来上がっていたためだ。
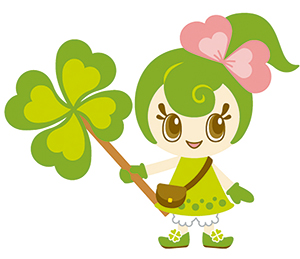
営業車や重機をはじめ解体現場の養生、
立入禁止のバリケードなど、さまざまなところに
掲示され、同社の活動を多くの人に
知ってもらうために一役買っている。
同社では20年ほど前から全工場で年2回、社員ボランティアによる地域の清掃活動を実施している。地元の自治会と合同で実施することもあり、社員と地域の住人との交流が生まれた。親しくなった人たちから夏祭りに招待されることもあるという。地元の小学校からの工場見学も積極的に受け入れる。岡部工場では、トラックが住宅地を通るため、できるだけ低速で走行することをドライバーに徹底するとともに、地元の住人にも「乱暴なドライバーがいたらぜひ車のナンバーを教えてほしい」と頼んだ。すると、「ナンバーを覚えるのは難しいから、ドライバーの名前をトラックに掲示してほしい」と要望があり、全車両でダッシュボードにドライバーの名前を掲示するようにした。地元と良好な関係を築くためには、こうした日ごろからの交流が欠かせない。
社員の意識も少しずつ変化している。これまで最終処分場で埋め立てされていたものが、燃料となって再利用できれば社会貢献につながるし、会社の利益にもなる。自社の素材をRPFに生かすためにはどうすればいいか、社員一人ひとりが考えるようになった。
日本では比較的ゴミの分別などが進んでおり、業者もルール通りに処分を行い、廃棄物処理に関しては大きな問題は起きていない。それを一歩進めて、廃棄物を有効活用する方法を模索することで、さらに一歩進んだ取り組みが可能になる。同社はそのモデルケースともいえる存在だ。
- 主な事業内容:
- 産業廃棄物の収集運搬・中間処理、RPFの製造など
- 所在地:
- 静岡県浜松市
- 社長:
- 藤城太郎
- 従業員数:
- 300名
機関誌そだとう202号記事から転載