一歩踏み出した先に、広がった未来
CASE②株式会社三友製作所
三友製作所は、医療用分析装置関連製品と電子顕微鏡用付属品の製造、そして半導体故障解析用ツールの設計・開発・製造を行っている企業である。同社の加藤木克也社長は、創業からの歴史を次のように振り返る。
「当社は1946年創業で、私の父が戦後、製造業の会社として立ち上げました。茨城県常陸太田市という土地柄もあり、日立製作所との取引が大きなウエイトを占めています。高度経済成長期には、同社の化学プラントなどで使われる工業計器を製造し、事業を拡大していきました」
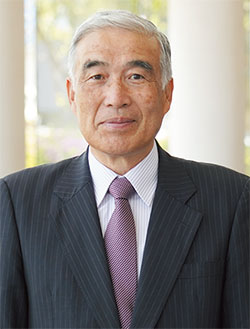
加藤木克也社長
- 主な事業内容:
- 電子顕微鏡関連付属品の製造、半導体故障解析ツールの製造、精密機械加工、分析機器関連製品の製造
- 本社所在地:
- 茨城県常陸太田市
- 創業:
- 1946年
- 従業員数:
- 280人
しかし、昭和の終わり頃になると、日本では化学プラントがつくられなくなり、工業計器の需要は縮小していってしまう。そこで、次に手がけたのが、日立製作所の那珂工場(現・日立ハイテク)で使われる理化学機器だった。
「日立製作所からいろいろな支援を受けながら、理化学機器へと移行したのが昭和から平成に変わる頃です。最初に扱ったのは、液体クロマトグラフィーという製品でした。薬品や飲料など、液体なら何でも分析できる汎用的な機器です」
ここから、現在、売上の大半を占める医療用分析装置のユニット製造に展開することができたのだという。加藤木社長が父から会社を引き継いだのは1995年、44歳で経営者となった。当時の課題は、若い世代の従業員がほとんどいなかったことだと語る。
「当時、従業員の平均年齢は47~48歳で、若い人はなかなか入ってこないし、入ってきてもすぐに辞めてしまう。そうした世代がもっと魅力を感じるような、仕事や職場にしないといけないと思いました。そのためには委託製造だけでなく、自分たちで製品開発に取り組むことが必要だと考え、1996年頃から自社製品の開発をスタートしたのです」
最初に挑戦したのは、電子顕微鏡内マイクロマニピュレータの開発だった。茨城大学工学部の教授から提案を受けて、電子顕微鏡で対象物を見ながら微細な作業ができる、ステージ製作の技術開発に取り組んだ。
「当時、私たちが目指していたのは、電子顕微鏡を使って顕微解剖を行えるというものです。茨城大学の協力も得ながら完成した機器を、電子顕微鏡学会で展示すると『非常におもしろい』と評価されたものの、残念ながら1台も売れませんでした。医学の世界において顕微解剖は時代遅れで、すでに遺伝子やDNAの研究が盛んになっていたからです」
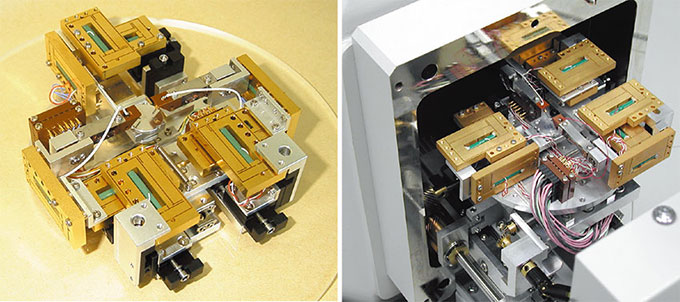
(写真左)2001年3月に完成した、半導体故障解析に特化したマイクロマニピュレータ。
(写真右)電子顕微鏡に組み込んで使う。
臆せず踏み出したのは、新たな事業へと続く道
一方で、マイクロマシン展という別の展示会にも、電子顕微鏡内マイクロマニピュレータを出して紹介していた。これを見た来場者が「この技術は、半導体の故障解析にも応用できるんじゃないか」と提案。そのアイデアをもらい、半導体の故障解析用マイクロマニピュレータ開発へと方向転換した。実はこの1件が、のちに新たな事業の発展へとつながったわけだ。
「簡単にいうと、テスターを使ってサブミクロンの世界で位置を特定し、電流や電圧を測る機械です。これは実際にお客さまにも使ってもらえるようになり、日本機械学会関東支部では技術賞を受賞しました。ところが、最初は数十ミクロン幅の回路に針を当てればよかったものが、時代が進むにつれて数ミクロンと狭くなっていったわけです。より細い針を搭載しなければ測定ができなくなり、そこで開発が行き詰まりました」
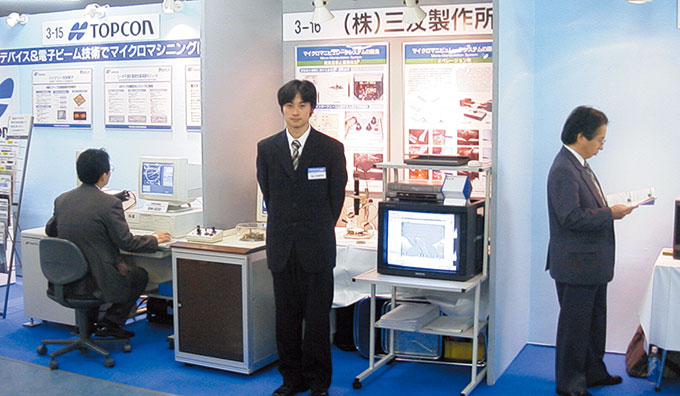
マイクロマシン展に出展したときの様子。
ここで、のちに大きく発展を遂げる新たなアイデアを得た。
当初は、強度と耐磨耗性の高い金属を細く針状にしたものの使用を検討していたが、細くしすぎると先端が曲がってしまい、使い物にならない。加藤木社長は解決策として、カーボンナノチューブ(以下、CNT)に注目した。今まで扱ったことのない素材であったため、茨城県内で行われた国立研究開発法人産業技術総合研究所(以下、産総研)主催のCNTセミナーに参加する。
「詳しく話を聞き、これなら私たちが目指しているテスターに採用できると思いました。そこで、CNTに関する情報提供や、製品化にあたって指導をしてもらえないかと、講師の方にお願いしたことが、産総研と共同開発を行うきっかけです」
結果として、CNTを使った開発はうまくいかなかったが、この相談を起点として、半導体の故障解析用プローブ開発を産総研と共同で続けていくこととなる。セミナーへの参加、そして産総研に開発の相談をしたことで、多少の方向転換はあったものの、現在まで続く社外連携の流れにつながったわけだ。まさに、三友製作所の未来に資するターニングポイントだったといえる。
ただ、多くの中堅・中小企業では、産総研をはじめとする研究機関など、普段接点のない相手へ相談することにハードルの高さを感じるかもしれない。加藤木社長もその1人だったが、実はそんなことはなかったと自身の経験を話す一方で、次のように指摘する。
「やはり、専門家への相談は効果的です。しかしながら、『困っているので、なんとかしてください』と丸投げしたり、受け身のスタンスで相談したりしても、今のような展開にはなっていなかったでしょう。課題やテーマを自社で明確にしたうえで、相談に臨むことが重要です。投げかける内容の論点が絞られていないと、受けるほうも何をアドバイスすればいいのかわからないでしょうから」
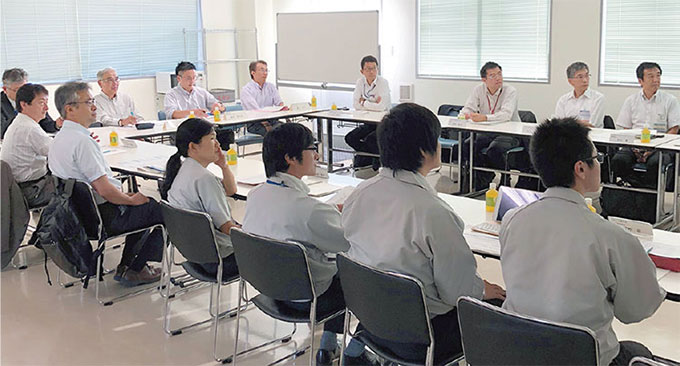
産総研との会議の様子。
当初は学ぶ立場だった三友製作所の技術者だが、今では双方向に議論がなされるほどに成長した。
自社にないリソースを、フル活用で実現する世界
半導体はさまざまなパターンをつくっていくため、試作段階では断線や異物混入などでのショートといった不良があるという。それを見つけて設計し直し、完成に向かっていくという工程において、開発スピードを上げるためには、問題の所在をいち早く特定することが重要になる。そこで三友製作所が開発したのが、EBAC解析用プローバだ。これは、半導体内配線に生じた断線不良・高抵抗不良を解析する手法で、同社が電子顕微鏡の分野で用いていた技術を半導体に応用したものだ。
「さらに、半導体関係のお客さまからの要望も聞きつつ、産総研と共同で、半導体の故障解析を行う高感度・多機能マルチプローバなども開発しています」
取引先である半導体を設計・開発する会社は、非常に速いスピードで技術が進歩していく。それに伴って故障解析を行う機器も、急ピッチで進化させていく必要が出てきた。例えば、EBAC解析の手法で見られる半導体の階層は、せいぜい上から2~3層が限界だ。しかし、10層以上あるパターンがどんどん開発され、それに対応しなければならない。
「深い層まで見たいのであれば、半導体の絶縁層を取ってしまえばいいだろうと考えました。プラズマ照射をして酸化膜を取り除くことは可能ですが、その後の分析をどうするかという課題も、産総研の知見をお借りしながら解決に至ったものです」
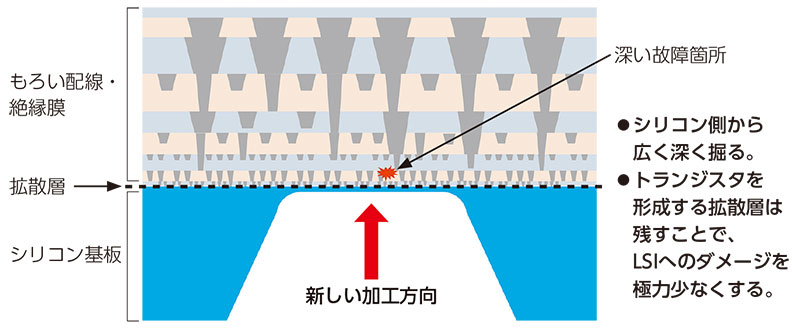
三友製作所が新たに開発した技術「薄膜化加工」の方法。
これにより、サブミクロン単位の配線でも故障解析が可能となる。
着手から約15年をかけ、三友製作所は産総研とともに、故障箇所だと特定した部分だけをエッチングする局所プラズマガンを開発。さらに、エッチングしたゴミ(残渣)が半導体上に残らないようにしたいと考え、機器先端から吐き出していたガスを、吸い込む方向に変えてみた。これにより、ゴミを吸い込みながらエッチングする独自技術「吸引プラズマ法」が誕生したのである。
「吸引プラズマ法で加工すると、残渣がありませんし、低い温度でエッチングすることが可能になったので、配線部分をそのまま残せるようになります。これは非常に有効な方法だということで、半導体開発の会社に使ってもらえるようになりました」
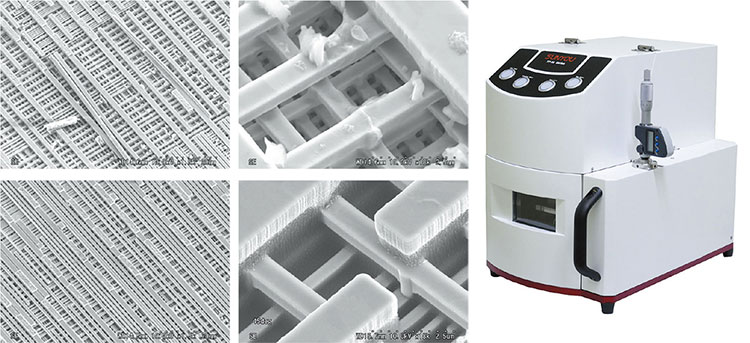
(写真左)上の2枚は従来法、下の2枚は吸引プラズマ法でエッチングを行った際の加工部分。
上2枚には剥離や残渣が見られるが、下2枚は非常にきれいな仕上がりだ。
(写真右)局所的なプラズマを照射し、試料の一部分のみを加工することができる卓上プラズマエッチング装置。
また、スケルトンEBAC解析法という、針を立てると下の層まできれいに見えて解析できる方法も、共同開発における大きな成果となった。
社外連携に一定の効果を感じた三友製作所は、次の段階として、吸引プラズマ加工実用化に向けた産学連携開発を行う。これには1台数億円の分析装置を使った評価が必要だが、同社にはない。いち中小企業では、なかなか実現できないことなのだ。
「私たちはこのような分析装置を持っていないし、知見もありません。お客さまから当社のプラズマ加工方法について性能などを聞かれても、エビデンスを出して説明できないのです。そこで産総研が『三友製作所が行っている方法で加工すると、こうなりますよ』という分析データを出し、評価してくれました。これは開発において、非常にありがたいことですし、自社ではできない重要な役割です」
さらに、吸引プラズマ法を半導体の故障解析にどう活かすかと考え、最下層のシリコンをきれいに取って、下からのぞくという手法で進めたのが、平成30年度のサポイン事業(戦略的基盤技術高度化支援事業、現Go-Tech事業)として採択された産総研との共同開発によって完成した、シリコンを削って、高いレベルできれいな面にする技術が決め手となり、採択に至ったという。
「これにより、面をきれいに磨くという技術を新たに獲得しました。それが今、非常に注目されているのです。私たちだけでは、サポイン事業の補助を受けることは難しかったので、この研究開発ができたのも、産総研との連携における大きな成果でしょう」
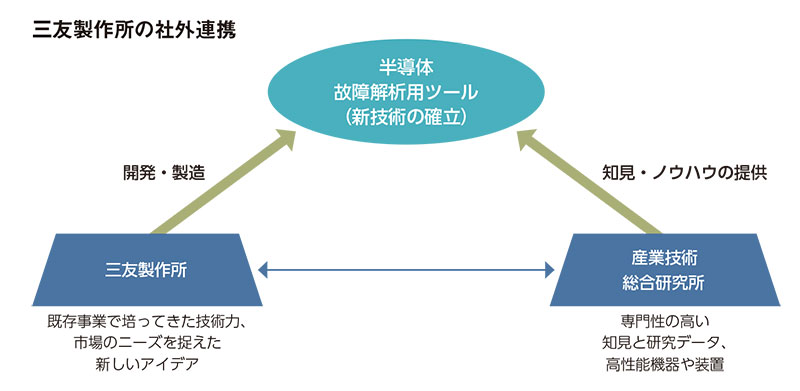
技術力向上や採用に、大きな意味があった
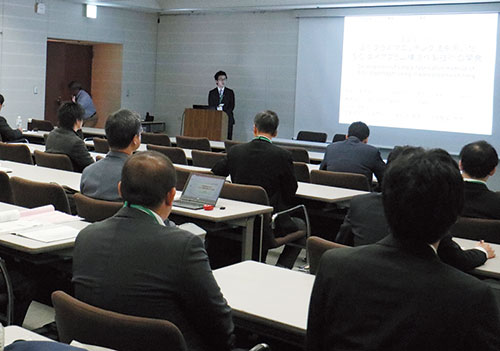
学会で発表を行う、三友製作所の技術者。
産総研との共同開発を行うことで、飛躍的に技術や知識のレベルが向上した。
産総研とのつながりは、製品や技術の開発以外にも会社にとって大きな価値があったと加藤木社長は語る。
「よかった点は、設計・開発を担う従業員の技術力が、飛躍的に向上したことです。当社が最初に開発を始めた頃は、ロボットをつくってみても今一つの出来だった。それが今では、当社の技術者が学会で発表するほどにもなってきましたし、産総研に行って学び続けていると、双方向でさまざまな議論ができるくらいに成長していて、レベルが非常に上がったと感じています。会社としては、実はこの効果がもっとも大きかったでしょう。最新情報や必要なデータも、いち早く得られます。半導体開発が今後どのような方向に向かっていくかということも含めて、さまざまな情報を知ることができました」
また、産総研以外にも、以前から連携していた茨城大学に加え、いくつかの大学とつながり、コラボレーションすることが増えたという。そこで三友製作所の事業に興味を持った大学生が、何名か社員として入社するという採用にもつながっている。
「今は医療用分析装置関連が大きな柱になっていますが、10年、20年、30年先を見据えて、もう1つ、柱となる事業が生まれてくるようにしたいです。産総研に限らず、一緒に研究開発を進められる連携先をこれからも探していきたいですし、当社が得た技術を半導体以外に使うことも考えながら、取り組んでいきます」
思い切って踏み出した一歩が、三友製作所の未来を切り拓く、大きな武器になっているのだ。
機関誌そだとう215号記事から転載